Introduction to Indium Bonding
Target bonding is a significant process that joins sputtering targets and backing plates together, yet improper bonding materials would lead to poor heat release, cracking, non-uniform deposition, and even de-bonding. Therefore, it is quite essential to have a basic understanding of the functions, benefits, and types of bonding in advance. This article is going to discuss these issues using the specific case of indium bonding.
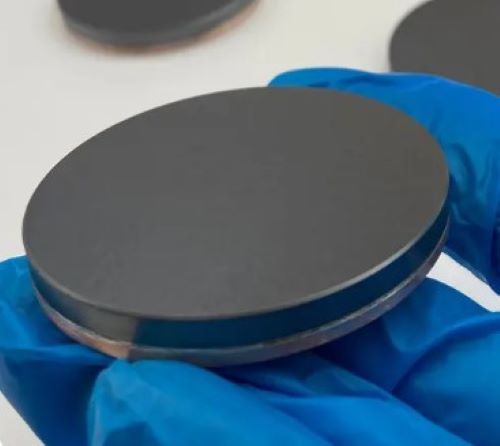
What Is Indium?
Indium has great ductility and thermal conductivity. It is a silvery-white post-transition metal that is the least abundant on earth. More importantly, indium is very soft with high plasticity and malleability. As for thermal properties, this soft metal has a conductivity of 86W/mK and a low melting point of 156°C. You can check the table below to learn more about the physical and chemical features of indium.
Table 1 Indium Properties
Features | Metric |
Density | 6.916 g/cm3 |
Melting Point | 156°C |
Boiling Point | 2000°C |
Tensile Strength | 4.50 MPa |
Modulus of Elasticity | 12.7 GPa |
Indium is applied to a range of industries. It is widely used to produce transistors and microchips for the semiconductor industry. A majority of indium is employed to make components for touch screens and solar panels because the metal bonds strongly to glasses.
Why Indium Is Chosen for Bonding Services?
Indium is suited for bonding services thanks to the following features.
- Special Structure
Indium has a tetragonal crystalline structure, which allows it to move “freely”. So there is no high stress when you put two dissimilar materials together using indium bonds. Consequently, there would be fewer cracks, de-bond, and breaks.
- High Conductivity
Indium is highly conductive for both electrical transfer and thermal cooling.
- Low Vapor Pressure
Indium has a low vapor pressure. It would not outgas in a vacuum environment.
Benefits of Indium Bonding
Indium bonding has the following advantages.
- Avoid Heat Problem
You can avoid overheating because bonded targets have better thermal conductivity and cool more efficiently.
- Prevent Cracking
In the sputtering process, most oxide and nitride targets withstand high pressures and high temperatures, which could cause severe problems. You can prevent cracks with proper bonding methods. Even if cracking appears, bonded targets and backing plates would stay together, and the sputtering process remains affected.
- Prolong Service Life
Bonding methods prevent other damages to your targets and prolong the targets’ life in the long term.
Other Types of Target Bonding
Indium bonding is a typical example of solder bonding, which is commonly used to set sputtering targets and backing plates together. Indium bond has the best electrical and thermal conductivity and notable malleability. The only limitation is that indium bonds melt at 156°C.
Apart from solder bonding, common bonding methods include epoxy bonding and elastomer bonding.
Epoxy Bonding can be operated at room temperature, so you don’t need to worry about the thermal expansion difference between targets and backing plates. It also works for large-area target bonding since there is no welding deformation. However, epoxy bonding has worse thermal conductivity compared with other bonding approaches.
Elastomer Bonding is applied to higher temperatures. It is an alternative to indium bonding since indium has a relatively low melting point of 156°C. Apply elastomer bonds if the sputtering targets are sensitive to temperature. Nevertheless, such bonds outgas for most polymer-based materials.
Related reading: Is it Necessary to Add Bonding Service for Your Sputter Targets?
Conclusion
Indium bonding can be applied to pure metal targets and ceramic targets to prevent overheating, cracking, and other damages. Epoxy bonding is conducted at room temperature. Elastomer bonding is suited for high-temperature applications. Stanford Advanced Materials is a supplier of various bonding services and sputtering targets. Check our website for more information.