1. Introduction
Sputtering is a key technology for thin-film deposition. It was first introduced in 1852 to deposit metals that couldn’t be applied through thermal evaporation. Over time, sputtering technology has advanced, leading to the development of magnetron sputtering.
Magnetron sputtering uses magnetic fields to control the movement of electrons. This improves the process by increasing ionization and creating a denser plasma. Within this system, there are two main types: balanced and unbalanced magnetron sputtering. Each type has unique features and is used for different purposes.
This article will explain the differences between balanced and unbalanced magnetron sputtering. We will also explore their working principles and applications.
2. What Is Magnetron Sputtering?
Magnetron sputtering is a method used to create thin films on various materials. It works by bombarding a target material with high-energy particles, usually ions from neutral gases like argon. These ions hit the target and cause atoms to be ejected. The ejected atoms then settle on a nearby surface, forming a thin film.
Magnetron sputtering improves the efficiency of this process by using magnetic fields. Magnets placed around the target trap electrons near its surface. This increases the ionization of the gas, creating a denser plasma. A denser plasma means more ions are available to strike the target, which leads to faster film deposition.
There are two main types of magnetron sputtering: balanced and unbalanced. These types differ in how the magnetic fields control the movement of electrons, affecting the way films are deposited.
3. Balanced Magnetron Sputtering
In balanced magnetron sputtering, the magnetic field lines are closed around the target. This keeps electrons trapped near the target surface. As a result, most of the plasma stays close to the target, and only a small amount of ion bombardment reaches the substrate.
Because the ions hitting the substrate have low energy, this method is useful when you need smooth and defect-free films. However, the low ion energy can sometimes lead to poor adhesion or lower density in the films. Balanced magnetron sputtering works well when the goal is to create thin, precise coatings with minimal damage to the substrate.
One downside is that if the substrate is too far from the target, the ion flux may not be strong enough to modify the surface. Applying bias voltage to the substrate can increase the ion energy, but this can also introduce stress and defects into the film.
Balanced magnetron sputtering is often used in the semiconductor industry where smooth, uniform coatings are required.
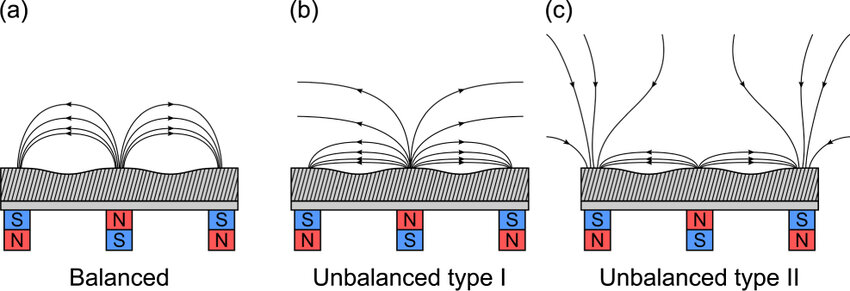
4. Unbalanced Magnetron Sputtering
Unbalanced magnetron sputtering allows more electrons to escape the magnetic trap. This creates a larger plasma area and increases ion bombardment on the substrate. In this setup, the magnetic field is not fully closed, so some electrons can travel further away from the target.
This increase in ion bombardment has several benefits. The high-energy ions improve film adhesion and make the film denser. It also allows for coating more complex shapes or larger substrates. The higher ion energy makes it possible to create harder and more wear-resistant coatings.
Researchers Window and Savvides classified unbalanced magnetron sputtering into two types. In Type 1, the central magnet is weaker, allowing more electrons to reach the substrate. This setup is commonly used in industries that need strong, durable coatings. Type 2 has a stronger central magnet but is less used because it provides fewer ions at the substrate.
Unbalanced magnetron sputtering is widely used for hard coatings like titanium nitride (TiN) or diamond-like carbon (DLC). These coatings are used in industries like automotive, aerospace, and tools where durability is key.
5. Comparison Between Balanced and Unbalanced Magnetron Sputtering
Balanced and unbalanced magnetron sputtering have several important differences. The main difference is in the amount of ion bombardment on the substrate. In balanced magnetron sputtering, the plasma stays close to the target, so the substrate receives less ion energy. This makes it better for films that need to be smooth and free of defects. However, the low ion energy can reduce film adhesion and density.
In unbalanced magnetron sputtering, the plasma extends beyond the target, allowing more electrons to reach the substrate. This leads to higher ion bombardment, which improves the film’s density and adhesion. This method is more suited for applications where a strong, durable coating is required.
Another key difference is in the deposition rate. Unbalanced magnetron sputtering tends to have a higher deposition rate because it generates a denser plasma. The increased ionization means more material is sputtered from the target, speeding up the coating process.
Balanced magnetron sputtering works best for applications that need uniform coatings with low defects, such as semiconductor manufacturing. Unbalanced magnetron sputtering is better for creating hard, wear-resistant coatings, like those used in cutting tools or aerospace components.
Feature | Balanced Magnetron Sputtering | Unbalanced Magnetron Sputtering |
Ion Bombardment | Low ion bombardment, low energy ions | High ion bombardment, high energy ions |
Plasma Distribution | Plasma stays close to the target | Plasma extends beyond the target |
Film Adhesion | Lower adhesion due to low ion energy | Higher adhesion due to higher ion energy |
Film Density | Lower density films | Higher density films |
Deposition Rate | Lower deposition rate | Higher deposition rate |
Applications | Uniform, low-defect coatings (e.g., semiconductor manufacturing) | Hard, wear-resistant coatings (e.g., cutting tools, aerospace components) |
6. Conclusion
Balanced and unbalanced magnetron sputtering offer different advantages depending on the application. Balanced magnetron sputtering is ideal when smooth, uniform films are needed, and ion bombardment should be kept low. Unbalanced magnetron sputtering, on the other hand, is better for producing strong, durable coatings with higher ion energy.
The choice between these two methods depends on the specific needs of the project. For delicate substrates or films that need to be free of defects, balanced magnetron sputtering is the best option. For hard, protective coatings, unbalanced magnetron sputtering offers the durability and strength required.
As industries continue to demand more advanced coatings, unbalanced magnetron sputtering is expected to become more important, especially for applications needing high-performance materials.