Introduction
In the world of thin film deposition, precision and efficiency are not just goals—they are essential to driving innovation. From electronics to optics, the choice of sputtering targets plays a pivotal role in the quality and performance of the final product. Among the different types of sputtering targets available, rotatable sputtering targets have emerged as groundbreaking tools. These innovative targets offer distinct advantages that are reshaping thin film technology. In this article, we will explore how rotatable sputtering targets work, their benefits, and how they are revolutionizing industries such as semiconductor manufacturing, optics, and more.
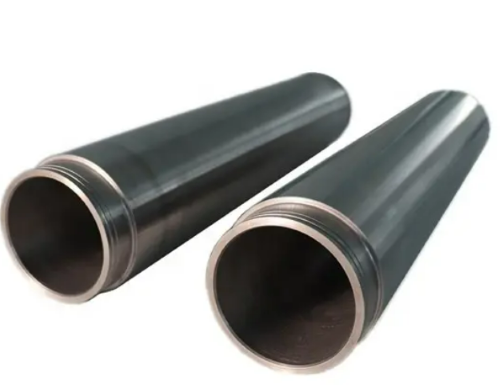
The Science Behind Sputtering: How It Works
Sputtering is a widely used physical vapor deposition (PVD) technique that allows thin films of various materials to be deposited onto substrates. In this process, high-energy ions bombard a solid target material, causing atoms or molecules to be ejected from the surface. These particles are then deposited as a thin film on the substrate, creating functional coatings with tailored properties.
Sputtering technology is employed in a variety of industries, from semiconductor manufacturing and optics to data storage and decorative coatings. It is valued for its ability to produce high-quality, uniform, and precisely controlled thin films. The choice of sputtering target material is crucial, as it directly influences the film’s composition, thickness, and adhesion properties.
Rotatable Sputtering Targets: The Next Step in Thin Film Innovation
Traditional sputtering targets were fixed, either as stationary disks or rectangular shapes. While functional, they had limitations, especially in maximizing target utilization and ensuring uniformity during deposition. This is where rotatable sputtering targets come into play, offering a dynamic solution to these issues.
Rotatable sputtering targets are designed to spin or rotate during the sputtering process. This movement introduces several key advantages:
- Enhanced Target Utilization: Unlike fixed targets, where erosion tends to occur in localized areas, rotatable targets distribute the wear and tear more evenly across the surface. This leads to better target utilization, less material wastage, and extended target lifetimes.
- Uniform Film Deposition: The rotation ensures that sputtering occurs from different areas of the target, promoting more uniform film deposition. This consistency is critical in applications where precise film thickness and composition are essential.
- Improved Coating Quality: The enhanced uniformity results in higher-quality coatings, which is particularly important in industries like semiconductors, where high precision is required, and optics, where optical performance is key.
- Increased Productivity: Rotatable targets support higher sputtering rates and improved process stability, meaning less downtime for target replacements and higher overall productivity.
Related reading: Planar Targets VS. Rotatory Targets: Advantages and Disadvantages
Applications of Rotatable Sputtering Targets
The versatility of rotatable sputtering targets is transforming a wide range of industries. Here are some key applications:
- Semiconductor Manufacturing: Rotatable targets are crucial for depositing thin films onto semiconductor wafers, enabling the creation of conductive, insulating, and barrier layers in integrated circuits. Their uniformity and efficiency ensure high precision in the production of microchips.
- Optical Coatings: In precision optical coatings, such as anti-reflective layers on lenses and mirrors, rotatable sputtering targets help achieve uniform film thickness and ensure the desired optical performance.
- Data Storage: Rotatable sputtering targets are used to produce thin films with high magnetic coercivity and storage density, which are essential in the production of data storage devices like hard disk drives and magnetic tapes.
- Decorative Coatings: These targets are also used in producing decorative coatings on materials like glass, ceramics, and metals, enhancing both aesthetic appeal and resistance to corrosion.
Future Trends in Thin Film Deposition
As industries continue to push for miniaturization and increased performance, the demand for precision in thin film deposition is only set to grow. Rotatable sputtering targets will play an even more pivotal role in achieving these goals. With continued advancements in materials science, these targets may evolve to accommodate new materials and even higher deposition rates, paving the way for next-generation technologies in electronics, optics, and renewable energy.
Conclusion
Rotatable sputtering targets have truly transformed thin film deposition technology. Their ability to improve target utilization, ensure uniform deposition, and increase productivity makes them indispensable across a wide array of industries. As technology continues to evolve, their role in achieving high precision and efficiency will only become more significant, paving the way for further breakthroughs in semiconductor fabrication, optics, data storage, and beyond.
Discover a variety of high-quality rotatable sputtering targets at Stanford Advanced Materials (SAM) , where cutting-edge technology meets reliability to drive your research or business forward.