Introduction
Physical Vapor Deposition (PVD) and Chemical Vapor Deposition (CVD) are prominent coating processes used in various industries to enhance the surface properties of materials. These processes provide protective and functional coatings that improve hardness, wear resistance, and other surface characteristics. This article provides an extensive comparison between PVD and CVD, delving into their mechanisms, applications, advantages, and limitations.
1. Overview of Deposition Techniques
Physical Vapor Deposition (PVD)
Process: Physical Vapor Deposition (PVD) involves the physical transfer of material from a solid or liquid source to a substrate in a vacuum environment. Common techniques include sputtering and evaporation.
Mechanism: Material is vaporized and then condensed onto the substrate, forming a thin film.
Types of PVD:
- Sputtering: Material is ejected from a target by ion bombardment.
- Evaporation: Material is heated until it vaporizes and then deposits on the substrate.
Sputtering involves bombarding a target material with high-energy ions, causing atoms to be ejected and deposited onto the substrate. This method is versatile, allowing for precise control over the film composition and thickness. Evaporation, on the other hand, uses thermal energy to vaporize the material, which then condenses onto the substrate. This process is simpler but may require higher temperatures and is less precise in controlling film properties compared to sputtering.
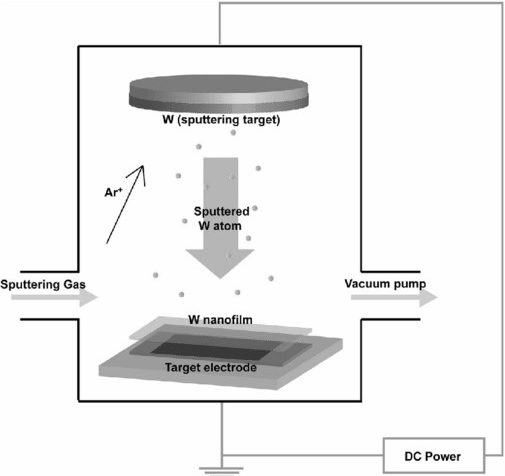
Chemical Vapor Deposition (CVD)
Process: Chemical Vapor Deposition (CVD) uses chemical reactions to deposit a solid material from a gaseous precursor onto a substrate.
Mechanism: Reactive gases interact at the substrate surface, forming a solid film through chemical reactions.
Types of CVD:
- Thermal CVD: Uses heat to drive the chemical reactions.
- Plasma-Enhanced CVD (PECVD): Uses plasma to enhance reaction rates at lower temperatures.
Thermal CVD involves heating the substrate and the gaseous precursors, causing the desired reaction to occur at the substrate surface. This method is widely used in the semiconductor industry due to its ability to produce high-purity films. Plasma-Enhanced CVD (PECVD) introduces plasma to lower the reaction temperature, making it suitable for coating heat-sensitive materials. PECVD also allows for better control over film properties and deposition rates.
2. Process Conditions
PVD Conditions
Temperature: Typically lower than CVD, ranging from room temperature to 500°C.
Pressure: Performed in a high vacuum environment (10^-2 to 10^-6 torr).
Substrate Preparation: Requires thorough cleaning to ensure good adhesion.
The lower operating temperatures of PVD make it suitable for coating temperature-sensitive substrates, such as polymers and certain metals. The high vacuum environment minimizes contamination and allows for the deposition of high-purity films. Proper substrate preparation is crucial to achieving strong adhesion and uniform coatings, often involving cleaning, etching, and sometimes heating the substrate.
CVD Conditions
Temperature: Higher than PVD, usually between 500°C and 1100°C.
Pressure: Can be atmospheric or low pressure.
Substrate Preparation: Involves similar cleaning processes but can tolerate more surface imperfections due to chemical reactions.
Details: The higher temperatures required for CVD processes facilitate the necessary chemical reactions but limit the types of substrates that can be coated. Low-pressure CVD (LPCVD) is often used to enhance the quality and uniformity of the coatings, while atmospheric pressure CVD (APCVD) can achieve higher deposition rates. Despite the stringent cleaning requirements, CVD can accommodate some surface imperfections since the chemical reactions can effectively coat irregularities.
Further Reading: Temperature Differences between PVD and CVD
3. Material Compatibility
PVD Materials
Metals: Titanium, gold, silver, etc.
Ceramics: Titanium nitride (TiN), aluminum oxide (Al2O3).
Others: Alloys, composites.
PVD is highly versatile, and capable of depositing a wide range of materials including metals, alloys, and ceramics. This versatility makes PVD suitable for applications requiring specific material properties such as hardness, conductivity, and corrosion resistance. For instance, TiN is commonly used for its high hardness and wear resistance, while aluminum oxide is valued for its insulating properties.
Further Reading: PVD Thin Film Deposition Materials List
CVD Materials
Metals: Tungsten, tantalum.
Ceramics: Silicon carbide (SiC), diamond.
Others: Polymers, composites.
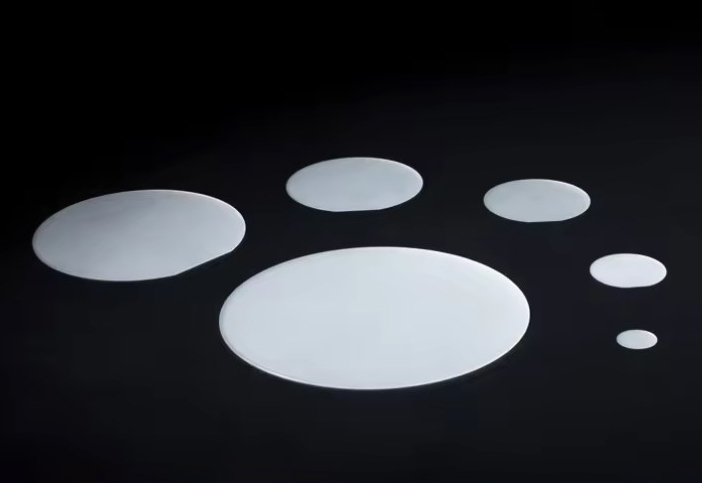
CVD excels in depositing materials that require high purity and precise stoichiometry, such as tungsten for its high melting point and electrical conductivity, and silicon carbide for its thermal and mechanical properties. The ability to deposit diamond films opens up applications in cutting tools and wear-resistant coatings. CVD can also produce composite materials by co-depositing different elements to achieve tailored properties.
4. Applications
PVD Applications
Tool Coating: Enhances hardness and wear resistance of cutting tools.
Decorative Coatings: Provides aesthetic finishes on jewelry, and watches.
Optical Coatings: Used in lenses, and mirrors for improved reflectivity.
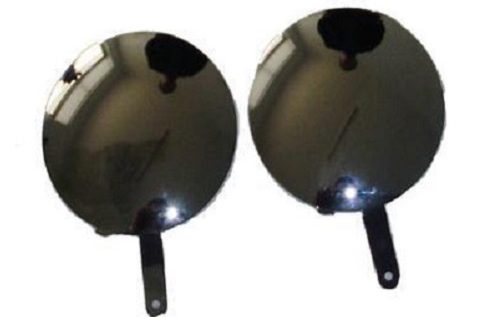
PVD is widely used to improve the performance and longevity of cutting tools by providing hard, wear-resistant coatings. Decorative coatings applied via PVD not only enhance the appearance of products but also add a layer of protection. In the optical industry, PVD coatings are used to create anti-reflective surfaces, improving the efficiency and clarity of lenses and mirrors. The ability to apply these coatings precisely and uniformly makes PVD a preferred method for high-performance and high-precision applications.
CVD Applications
Semiconductor Industry: Deposition of silicon nitride, and silicon dioxide.
Protective Coatings: Corrosion-resistant coatings on turbine blades.
Medical Devices: Biocompatible coatings for implants and instruments.
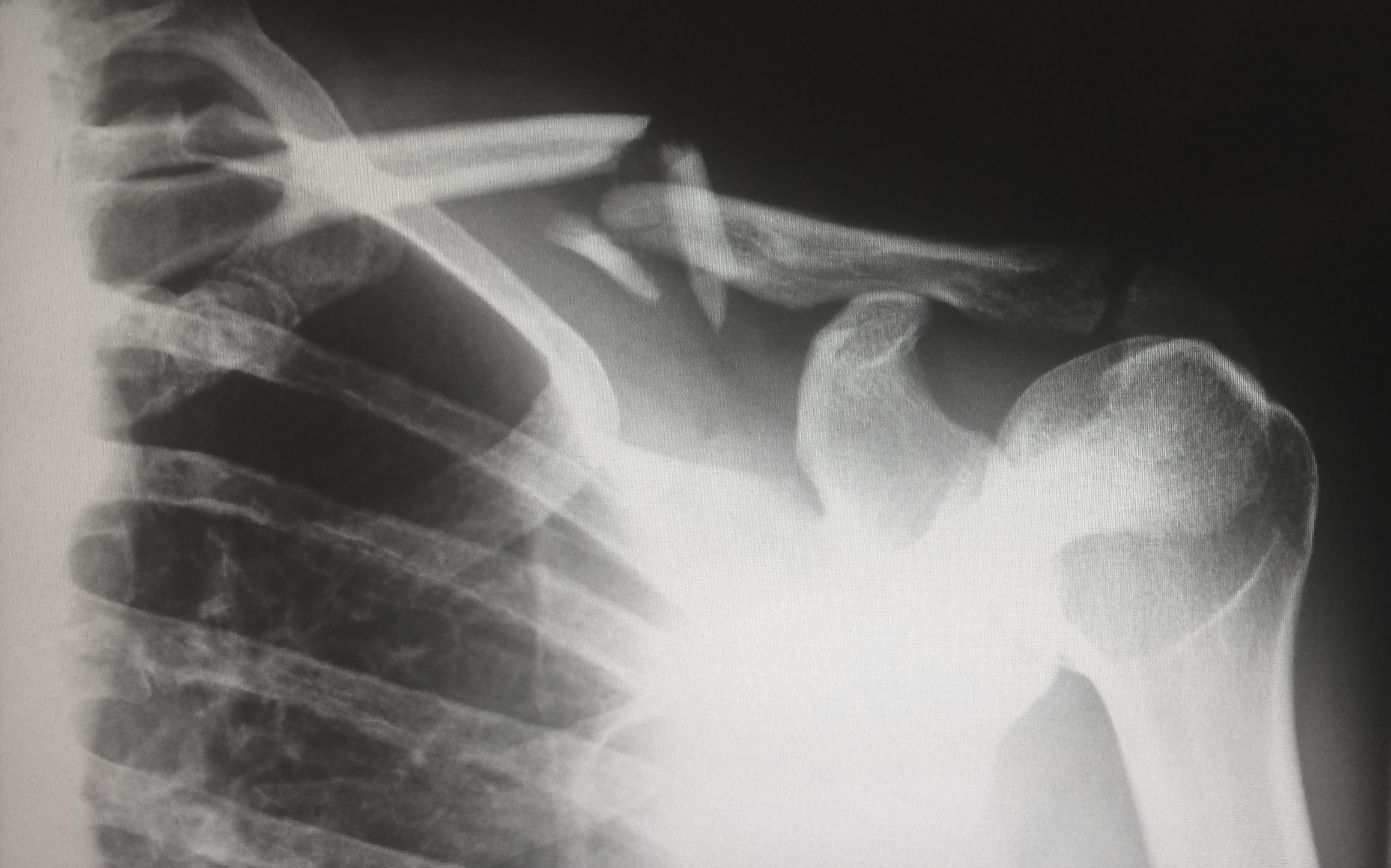
CVD is integral to the semiconductor industry, providing high-quality dielectric and conductive films essential for device fabrication. Protective coatings deposited by CVD are used to enhance the durability and lifespan of turbine blades in high-temperature and corrosive environments. In the medical field, biocompatible coatings such as titanium nitride improve the performance and longevity of implants and surgical instruments. CVD’s ability to deposit uniform and high-purity films makes it a critical process in advanced technological applications.
5. Advantages and Disadvantages
PVD
Advantages:
- Produces Thin, High-Quality Coatings: PVD provides precise control over film thickness and composition, resulting in high-quality coatings with excellent properties.
- Environmentally Friendly: The process generates minimal waste and uses no harmful chemicals, making it eco-friendly.
- Operates at Lower Temperatures: Suitable for temperature-sensitive substrates, expanding its range of applications.
Disadvantages:
- Limited to Line-of-Sight Coatings: PVD can only coat surfaces that are directly exposed to the vaporized material.
- Requires High Vacuum Conditions: The need for a high vacuum adds complexity and cost to the process.
- Slower Deposition Rates: Compared to CVD, PVD typically has slower deposition rates, which can impact productivity.
PVD processes are advantageous for producing high-quality coatings with precise control over thickness and composition. The lower operational temperatures and minimal waste production make PVD an environmentally friendly option. However, the need for a high vacuum environment and the line-of-sight limitation can restrict the complexity of the shapes that can be coated. The deposition rates in PVD are generally slower compared to CVD, which can be a drawback in high-volume production scenarios.
CVD
Advantages:
- Capable of Coating Complex Geometries: CVD can uniformly coat intricate and non-line-of-sight surfaces, making it suitable for complex components.
- Produces Dense, High-Purity Coatings: The process results in coatings with excellent structural integrity and purity.
- Wide Range of Materials: CVD can deposit a variety of materials, including metals, ceramics, and composites.
Disadvantages:
- Higher Operational Temperatures: The high temperatures required limit the types of substrates that can be used.
- Potentially Hazardous Precursor Gases: The use of toxic and reactive gases necessitates stringent safety measures.
- More Complex Equipment and Maintenance: The process involves sophisticated equipment and higher maintenance requirements.
CVD is well-suited for coating complex geometries, making it ideal for intricate components and internal surfaces. The dense and high-purity coatings produced by CVD enhance material performance in demanding applications. However, the higher temperatures required and the use of hazardous precursor gases necessitate careful handling and sophisticated equipment, increasing the complexity and cost of the process. Despite these challenges, the versatility and quality of CVD coatings make it a preferred choice for many high-performance applications.
6. Future Trends and Developments
Both PVD and CVD are continually evolving with advancements in technology and materials science. Future trends include:
- Nanostructured Coatings: These offer enhanced mechanical and optical properties due to their unique nanoscale structures. Researchers are developing methods to precisely control the nanostructure of coatings to improve hardness, wear resistance, and other surface properties.
- Hybrid Techniques: Combining PVD and CVD processes can optimize performance by leveraging the strengths of both methods. For instance, a hybrid approach can utilize the high-quality, dense coatings of CVD and the lower temperature, environmentally friendly aspects of PVD.
- Environmental Considerations: There is a growing focus on developing greener processes with reduced toxic by-products. Innovations are aimed at using safer precursor materials and optimizing processes to minimize environmental impact.
- Advanced Materials: The ongoing exploration of advanced materials, including carbide ceramics and other high-performance ceramics, is driving new applications in various industries. These materials offer superior properties such as high hardness, thermal stability, and chemical resistance, making them ideal for next-generation coatings.
- Integration with Nanotechnology: The integration of nanotechnology with PVD and CVD processes holds promise for creating coatings with unprecedented properties. Nanocoatings can provide ultra-thin, yet highly durable layers that enhance the performance and longevity of components.
Conclusion
Physical Vapor Deposition (PVD) and Chemical Vapor Deposition (CVD) offer distinct advantages and are suited for different applications based on their unique properties and process conditions. Understanding these differences allows for informed decisions in selecting the appropriate coating method for specific industrial needs.
As technology advances, the development of new deposition techniques and the enhancement of existing ones will likely continue. Research into improving the synthesis and application processes of these materials could lead to even more robust and efficient solutions for industrial challenges. The ongoing exploration of nanotechnology and its integration with deposition techniques holds promise for the next generation of high-performance coatings. Stanford Advanced Materials (SAM) offers sputtering materials and evaporation materials for both PVD and CVD coating processes, ensuring that industries have access to the best resources for their coating needs.