In the sputtering process, it is important to protect the sputter targets from damages, and a very good way to achieve this is by subjecting the sputter targets to bonding services. In this post, we’ll dive deeper into the meaning and importance of target bonding services, as well as the different types of target bonding services used in the sputtering process.
What is the Target Bonding Service?
Target bonding is an important process in target sputtering in which solder is used to bond sputtering targets to a backing plate. There are different methods of carrying out target bonding, but the most important thing about these bonding services is that they help to shield the sputtering targets from warping, cracking, and other damages during the sputtering process.
In its most basic form, the sputtering target bonding process provides the metal bonding needed to affix sputtering targets to backing plates. This is essential for systems that do not use a bolt-on target assembly. Usually, the sputtering targets are placed in the sputtering source cathode within the sputtering deposition system. Since the system works at higher power, the target’s surface generates plenty of heat. The heat is drawn by the solder layer from the target’s surface into the backing plate.
This heat is finally transferred through the piece of the backing plate and removed by the cooling assembly which is also included in the system. The target bonding process creates an interface thermal integrity between the cooling assembly and the surface of the sputter. This helps to increase the lifespan for targets to tolerate most heat. The most commonly used target bonding services are indium bonding and elastomer bonding. Below, we discuss these in detail.
Types of Bonding Services
Indium Bonding
Indium involves bolding two or more sputtering targets with indium or one or more sputtering targets using an indium plate. Usually, indium bonding is used in target bonding because of the following benefits:
- Indium has very good thermal and electrical conductivity. This helps it to efficiently eliminate plenty of heat from the sputtering targets.
- You can break the indium bond apart, so that the backing plate can be reused, thereby helping you save costs.
- Indium is more malleable than other bonding materials. This feature enables it to minimize the risk of cracking often caused by the mismatch of targets and backing plate in thermal expansion coefficients.
Note that the indium bonding service can be limited since it doesn’t easily take heat above 150°C. In fact, temperatures above 156.6°C will cause the indium bond to melt and separate from the sputtering targets. In this case, other more heat-resistant bonding services can be used in place of indium bonding. Indium bonding seems to work best for pure metal sputtering targets and ceramic sputtering targets.
OFHC Copper Backing Plates
OFHC means oxygen-free, copper backing plate is a commonly used backing plate during target bonding. OFHC copper backing plate is usually used for bonding ceramic targets, as it lacks magnetic properties and has a low coefficient of thermal expansion. This backing plate also has good electrical characteristics.
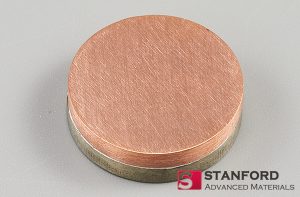
It is mostly used because it is easy to machine, manipulate, and is affordable. Other types of backing plates used for bonding services are copper, molybdenum, and copper-chromium. Note that the backing plates are an essential component in sputtering the target, as they are used to mount the target to the tool.
The backing plate also enhances the mechanical strength of the target and facilitates the cooling process.
Elastomer Bonding
Elastomer bonding is typically used in place of indium bonding, especially when the application involves a higher temperature. Elastomer bonding is known for the following:
- Applications in situations where indium bonding consistently melts during work.
- When the elastomer bond does not absorb any moisture, and it can efficiently handle the cycled between vacuum and atmosphere.
- It is used when the sputtering targets are fragile with low melting points and density and are sensitive to high temperatures. This often requires that the elastomer bonding be done at a low temperature, typically between 50-100°C to prevent damage to the sputtering and the bonding process.
Note also that the elastomer bonding service outgases in a vacuum chamber for bonding involving polymer-based materials. Sputtering targets that often require elastomer bonding include pure metal sputtering targets, such as:
- Indium sputtering target
- Bismuth sputtering target
- Lithium sputtering target
- Selenium sputtering target, and
Oxide sputtering targets, such as:
- Cobalt Oxide sputtering target
- Tin Oxide sputtering target
- Strontium Titanate
- Lithium Orthophosphate sputtering target
- Barium Strontium Titanate
- Lithium battery materials targets
Advantages Target Bonding Services
- It allows for the optimization of the target thickness to save costs for the metals. For instance, the material allows the transfer of heat through it to be faster when the material is thinner. This is where the importance of the copper backing plate becomes very obvious.
- It helps in providing planar and tubular targets, which technically, cannot be manufactured as individual parts
- Target bonding allows a ceramic material to cool more efficiently. This is because the target is in close contact with the conductive solder layer, which draws the heat from the target surface into the copper backing plate.
- Prevention of cracking and warping of ceramic sputtering targets during sputtering.
Conclusion
Target bonding services are essential for a successful sputtering process, mostly for systems that do not use a bolt-on target assembly. However, you want to be sure that the bonding service you are using is best suited for the particular targets in question.
Thank you for reading our article and we hope it can help you better decide whether your sputter targets need bonding services. If you want to know more about sputteing materials, we would like to advise you to visit Stanford Advanced Materials (SAM) for more information.