1. Introduction to Sputtering Target Selection
The target quality is rather significant for the coating process, and targets’ features are affected by a variety of parameters like purity, density, porosity, grain sizes, shapes, etc. The better the target quality is, the better performance we have, and the firmer the coating layers are. Here we will discuss the details of how these characteristics of sputtering targets influence coating quality in this article.
2. How Does Target Purity Affect Coating Quality?
Purity is one of the key factors affecting coating quality because impurities would cause lots of problems for the sputtering process.
Generally, there are mainly 3 kinds of impure content in the coating-making process– impurities in solids, oxygen, and water vapor. If these materials enter the vacuum chamber, they could not adhere to the surface of the substrate. Consequently, several coatings would not be firmer enough as expected, and they would even peel off. Therefore, effective measures should be taken to acquire high-purity targets.
Let’s further explain the danger of impure content with the specific case of the copper target. A small amount of sulfur is usually introduced to obtain suitable grain sizes for the target. However, if the sulfur content exceeds 18 ppm, micro-cracks can appear in the target, and discharge comes. Impurities could lead to cracks and discharges for Si-Al targets as well. Therefore, we’d better use high-quality targets with purity as high as possible.
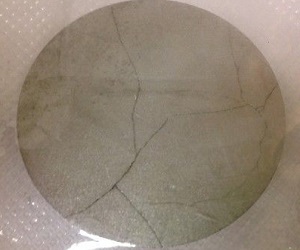
Further reading: Effect of Sputtering Target Purity on Large-Area Coating Production
3. How Does Target Density Affect Coating Quality?
Target density is another crucial factor affecting coating quality.
The density of target pieces not only has a great influence on their performance in the sputtering process but also determines the electrical and optical features of films. Additionally, high-density targets are needed to withstand the high temperature and pressure in the chamber. Actually, the casting target’s relative density should be over 98%, and the powder metallurgy target is supposed to exceed 97%. The relative density should be more than 90% generally.
Porosity also matters, and it is closely related to target density.
Low-density target materials usually have a loose and porous structure, which introduces high oxygen content and other impurities. Hence, the whole coating-making process is contaminated. Cracks and discharge situations happen consequently. Materials might be burnt out sometimes. Therefore, high-density target materials should be employed to prevent these problems.
4. Other Factors Affecting Coating Quality
There are many more elements influencing the coating preparation.
- Grain sizes: The target grain size ranges from microns to millimeters. Targets with smaller grain sizes relatively have a faster sputtering rate, because the grain boundaries of these refined targets are more vulnerable to attack in the coating production process.
- Shapes: There are planar targets and rotatory targets available for large-area coating. The target shape affects the stability and utilization rate of the target.
- Uniformity: Uniformity is quite essential because uneven distributions of materials can cause numerous problems. Both the sputtering rate and the film quality will be affected.
Further reading: What Are the Primary Performances Requirements of Target Materials?
5. How to Control Them during the Production Process?
5.1 Control the Parameters in the Manufacturing Process
Different methods are used to control these parameters in the manufacturing process. We are going to discuss these methods in the case of ITO (Indium Tin Oxide) sputtering targets.
- Vacuum hot pressing: This means could produce high-density targets of 91-96%. The coating material is made as follows. First, add samples to the heated mold. Then, modify the model under controlled temperatures. A finished product would be obtained after consequent melting, hardening, and cooling.
- Hot isostatic pressing (HIP): HIP can increase the density of targets at a relatively low temperature. You need to reduce the ITO solid solution powder in a certain reducing atmosphere and a temperature of 300 to 500 °C.
- Cold isostatic pressing (CIP): CIP makes ceramic targets with a density of 95%. It uses liquid as a pressure medium to transfer high pressure.
We should also keep the temperature, pressure, operation time, and inert gases used in the whole process for better performance of sputtering targets.
5.2 Choosing a Trustful Sputtering Target Supplier
Meanwhile, you can get high-quality sputtering targets from trusted suppliers if you need a small number of certain targets for business or research. Large orders are also welcomed. 3 qualified target suppliers are listed here.
- Stanford Advanced Materials (SAM): Stanford Advanced Materials provides high-quality sputtering targets at reasonable prices. The website www. sputtertargets.net offers more detailed specifications for all sputter target products and services.
- Refining Systems: Refining Systems offers high-quality targets with high purity from 99.5% to 99.999%. Technologies like flat lapping, polishing, and stamping are employed for better targets.
- Phelly Material USA: Phelly Material USA is an ISO 9001:2000 certified manufacturer with a wide array of sputtering targets. Evaporation materials are also available.
6. Conclusion
Diverse elements like purity, density, porosity, grain sizes, and shapes should be controlled for better target performance in the coating production process. Getting a trusted manufacturer or supplier can also be helpful. Hope that you can get a better understanding of how to select targets for coating materials. Please contact us or visit our site for more information.