Thin-film transistors (TFTs) are fundamental components in a myriad of electronic devices that shape our daily lives, from the vibrant displays of smartphones and TVs to the essential functionality of touch screens and solar cells. Central to the fabrication of these versatile transistors is the use of magnesium oxide (MgO) targets, a critical material in the sputtering processes that deposit thin films. The unique properties of MgO enhance the performance and durability of TFTs, marking it as a superior choice in semiconductor manufacturing. This article delves into the pivotal role of MgO targets in TFT production, discussing their advantages over traditional materials and highlighting their potential to revolutionize the future landscape of electronic devices.
Understanding Thin-Film Transistors
Thin-film transistors (TFTs) serve as essential switches within a multitude of electronic devices, orchestrating the flow of electrical current across circuits. At their core, TFTs control the electrical current between two points: the source and the drain. This functionality is crucial for operating the pixel arrays in displays, where each transistor dictates the illumination of individual pixels, thereby affecting overall image clarity and quality.
A typical TFT comprises several key layers:
- Semiconductor Layer: This is the active component where the charge carriers (electrons or holes) move. The choice of semiconductor material can significantly affect the transistor’s performance.
- Gate Electrode: Positioned above the semiconductor layer, separated by an insulator, the gate electrode is critical for the transistor’s operation. By applying voltage to the gate, it modulates the conductivity of the semiconductor layer, effectively turning the current flow on or off.
- Insulating Layers: These layers prevent direct electrical contact between the gate electrode and the semiconductor, and also protect the semiconductor from environmental factors that might degrade its performance.
Each layer’s interaction and composition are finely tuned to provide reliable and efficient performance, making TFTs indispensable in the fabrication of high-resolution, fast-refreshing electronic displays.
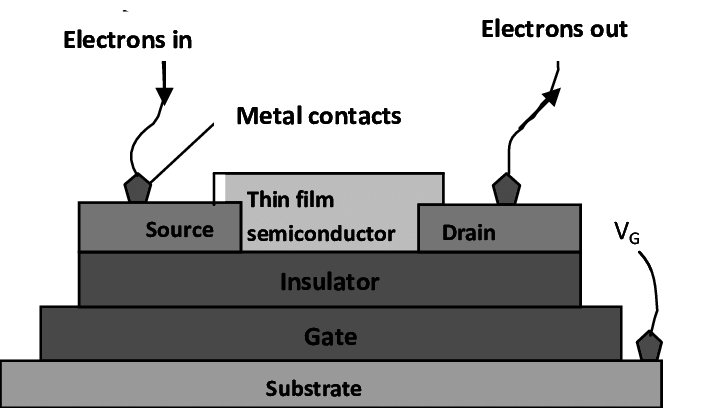
Limitations of Commonly Used Semiconductor Materials
In the production of thin-film transistors (TFTs), a variety of semiconductor materials are employed, each chosen for specific properties that enhance device functionality. Amorphous silicon, indium gallium zinc oxide (IGZO), and zinc oxide (ZnO) are among the most commonly used. Amorphous silicon is favored for its established use and cost-effectiveness, making it a staple in traditional displays. IGZO, noted for its high electron mobility, supports higher refresh rates and energy efficiency, which are critical for modern high-resolution displays. ZnO is valued for its excellent optical properties and transparency, suitable for various optical devices.
Despite their advantages, these materials exhibit significant limitations, particularly concerning their electrical performance and stability:
- Amorphous Silicon: While economical, it suffers from slower electron mobility compared to crystalline forms, limiting its use in high-speed or high-frequency applications.
- IGZO: Although it offers improved performance over amorphous silicon, IGZO can be unstable under certain environmental conditions, such as exposure to light and moisture, which can degrade the device over time.
- ZnO: Similar to IGZO, ZnO has issues with environmental stability and can also suffer from variability in electrical characteristics due to impurities or defects in the material.
These limitations are critical factors in the ongoing development of TFT technology, prompting the exploration of alternative materials like magnesium oxide (MgO) to overcome these drawbacks and enhance the overall performance and stability of TFTs.
Introduction to Magnesium Oxide Targets as a Superior Alternative
Magnesium oxide (MgO) is increasingly recognized as a superior material in the manufacturing of thin-film transistors (TFTs) due to its exceptional physical and chemical properties. Key among these properties is MgO’s high dielectric constant, which is crucial for gate dielectrics—the layers that separate the gate electrode from the semiconductor in a TFT. This high dielectric strength allows MgO to effectively maintain an electric field while minimizing the gate leakage current, a common issue with less robust materials.
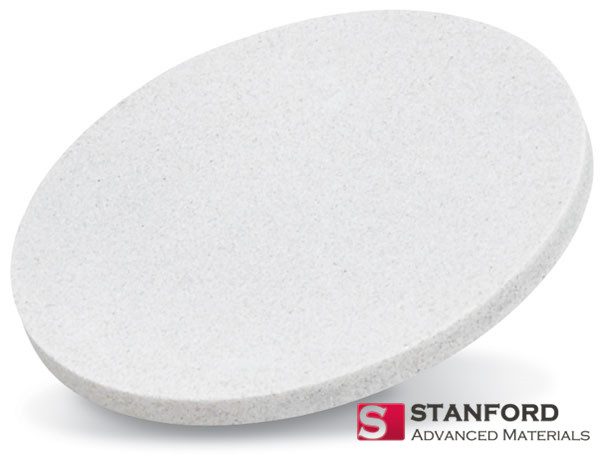
Additionally, MgO boasts a remarkably low leakage current, which is instrumental in enhancing the energy efficiency of electronic devices. By reducing the amount of current that unintentionally passes through the dielectric layer, MgO significantly improves the transistor’s overall electrical performance and stability. The use of MgO in TFTs involves deploying it as a buffer layer between the semiconductor layer and the gate electrode. This strategic placement not only optimizes the interface’s electrical properties but also contributes to the stability and longevity of the transistor by preventing degradation of the underlying semiconductor and insulating layers.
With these properties, MgO targets are crucial for advancing the capabilities and durability of TFTs, thereby playing a pivotal role in the evolution of electronic display technologies.
Comparative Advantages of MgO Over Other Insulating Materials
Magnesium oxide (MgO) distinguishes itself from traditional insulating materials like silicon dioxide (SiO2) and aluminum oxide (Al2O3) through several key advantages that enhance the performance and reliability of thin-film transistors (TFTs) and other electronic components. MgO’s high dielectric constant is one of its most significant benefits. This property allows MgO to hold and transfer more electrical charge per unit area than SiO2 or Al2O3, leading to improved electrical performance in devices. This increased charge capacity is crucial in applications requiring high efficiency and fast switching capabilities.
In terms of thermal stability, MgO excels in maintaining its structural integrity and performance even under high temperatures. This makes it an ideal choice for devices operating within harsh or elevated thermal environments, where materials like SiO2 and Al2O3 might degrade or fail, thereby compromising the device’s functionality and safety.
Furthermore, MgO’s low leakage current is another critical advantage. Lower leakage currents mean that less energy is wasted as heat, thus enhancing the overall energy efficiency of the device. This property is particularly important in reducing power consumption and heat generation in high-density electronic applications, such as in advanced computing and large-scale digital displays, where energy management is critical. This combination of high dielectric constant, superior thermal stability, and low leakage current makes MgO a superior material for use in sophisticated electronic applications, pushing the boundaries of what is possible in TFT technology.
Table 1. Comparative Advantages of MgO Over Other Insulating Materials
Property | Magnesium Oxide (MgO) | Silicon Dioxide (SiO2) | Aluminum Oxide (Al2O3) |
---|---|---|---|
Dielectric Constant | High: Enhances electrical charge capacity and performance | Moderate: Limited charge capacity and performance | Moderate: Limited charge capacity and performance |
Thermal Stability | Excellent: Maintains integrity and performance at high temperatures | Good: Can degrade under high temperatures | Good: Can degrade under high temperatures |
Leakage Current | Low: Reduces energy waste and enhances efficiency | Higher: Leads to increased energy waste | Higher: Leads to increased energy waste |
Implications for the Future of Electronic Devices
As the demand for high-performance electronics continues to increase, magnesium oxide targets will play a more critical role in the production of TFTs and other electronic components. The use of these targets guarantees the dependable and consistent performance of these devices, leading to enhanced efficiency and longevity.
Conclusion
Stanford Advanced Material (SAM) provides quality Magnesium oxide targets and pellets for a variety of applications. Hope that you can select the perfect wafers for your projects. For more information, please check our homepage.