Introduction
Purity is one of the prime performance requirements of target selection, which has been explained in our previous article. It takes countless money, time, and labor every year to separate impurities. However, do impurities always have a negative influence on sputtering? We are going to explore this question in this article with specific cases.
Importance of Purity in Target Selection
Impurities cause several problems in the sputtering process. For instance, we might get infirm coatings with targets of poor purities. The impure contents in the sputtering process include various forms, including solid, oxygen, and water vapor. The atoms ejected from the target materials would not adhere to the surface of the substrate with these impure contents. As a result, the coatings are not firm as expected, and might even peel off from the substrate.
Additionally, impurities lead to cracks and discharges. Once there are impurities that hinder heat transfer, cracks will appear. When the target has large obvious cracks, the charge is prone to concentrate at the edge of the cracks, and abnormal discharges take place. Take the case of the copper sputtering target. Adding a small amount of sulfur when sputtering copper targets can obtain better performance. However, if the sulfur impurities exceed 18 ppm, microcracking occurs.
Therefore, impurities are supposed to be reduced as much as possible.
Related reading: Effect of Sputtering Target Purity on Large-Area Coating Production
Deposition of ZrN Thin Films Using Zirconium Targets
Nevertheless, there are some special cases where impurities do not always have a negative effect. Depositing ZrN thin film is a perfect example. There is a range of methods to produce zirconium nitride films, one of which is using zirconium targets as the raw materials.
Zirconium is inevitably mixed with hafnium impurities
Zirconium is mixed with hafnium in nature. The main source of zirconium is zircon. Hafnium is a by-product of zirconium refining. The hafnium content in zircon compared to zirconium is around 1 to 50 [1].
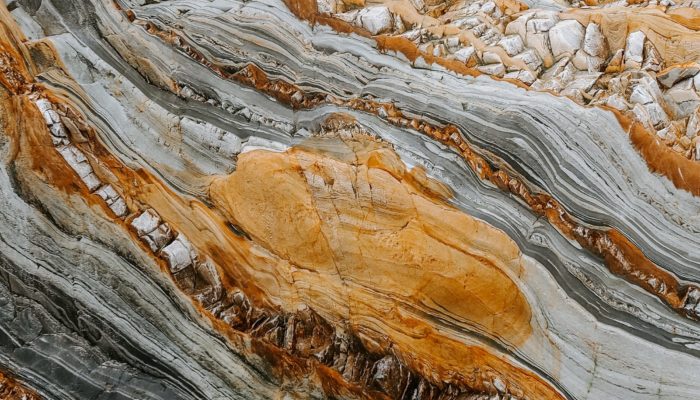
Zirconium is inevitably mixed with a tiny amount of hafnium impurity since they are difficult to separate from each other. Zirconium (Zr, 40) and hafnium (Hf, 72) locate in the same group in the periodic table. The two elements are similar in size and chemical features due to lanthanide contraction. Both of them are shiny, ductile, and chemically inert metals. You can check the table below and find more resemblance.
Table 1 Zirconium and Hafnium Properties
Zirconium | Hafnium | |
Melting Point | 1854°C, 3369°F, 2127 K | 2233°C, 4051°F, 2506 K |
Boiling Point | 4406°C, 7963°F, 4679 K | 4600°C, 8312°F, 4873 K |
Density | 6.52 g/cm3 | 13.3 g/cm3 |
Will hafnium impurity in the Zr target affect the coating?
As we mentioned above, zirconium is inevitably mixed with hafnium impurities. So will these impurities affect the film quality?
There is a contrast test made by Fernandez et al. studying the effect of hafnium contaminant present in zirconium targets on sputter-deposited ZrN thin films [2], and here is how they conducted the experiment.
- Make sure sputtering takes place in a chamber with argon, nitrogen, and hydrogen. Argon does not react with other materials; nitrogen reacts with zirconium targets to acquire ZrN coatings; hydrogen is used to reduce oxygen impurity.
- The percentage of hafnium contamination in the reference group is less than 1%. The hafnium contents of the control groups are 1.8%, 3.7%, and 5.5% respectively.
- Ultimately, the chemical properties are examined by RBS, SEM, and high-temperature oxidation tests. Astonishingly, the hafnium impurities contribute to the great strength and oxidation resistance of ZrN films at 773 K.
Thus, impurities do not always impose a negative impact on sputtering.
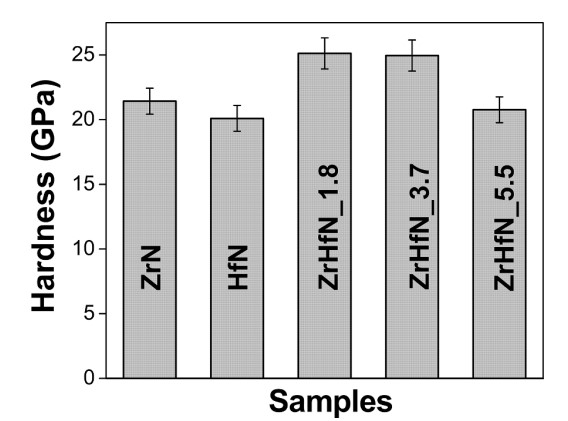
Sometimes hafnium should be separated from the Zr target
Although the impurity can contribute to the ZrN film, remember to separate hafnium from zirconium in nuclear applications since their neutron absorption ability differs widely. Zirconium does not absorb thermal neutrons. It also has outstanding corrosion resistance. So, Zr is applied to make metal components of nuclear reactors. Hafnium is notable for its large neutron absorption cross-section, which is 600 times that of zirconium. So, it is used to produce reactor control rods.
Related reading: Separation of Zirconium and Hafnium
Conclusion
Target purity is of great significance in the sputtering process, yet there are some special cases in that impurities do not have a negative effect. Hope that you can have a better understanding of target impurities and their influence on sputtering. Stanford Advanced Materials offers high-purity sputtering targets of different types. Send us an inquiry for more information, quick delivery, and competitive price.
Reference:
[1] EDISON (n.d.). Zirconium and hafnium. https://www.edisongroup.com/insight/zirconium-and-hafnium/23292/
[2] D.A.R. Fernandez, B.S.S. Brito, I.A.D. Santos, V.F.D. Soares, A.R. Terto, G.B. de Oliveira, R. Hubler, W.W. Batista, E.K. Tentardini, Effect of hafnium contaminant present in zirconium targets on sputter deposited ZrN thin films, Nuclear Instruments and Methods in Physics Research Section B: Beam Interactions with Materials and Atoms, Volume 462, 2020, Pages 90-94, ISSN 0168-583X, https://doi.org/10.1016/j.nimb.2019.11.005.