Introduction
Dielectric substrates are indispensable materials in modern electronic devices. They play a crucial role in supporting circuits, optimizing electromagnetic performance, and protecting components. As technology advances, dielectric substrates have evolved to include a diverse range of materials with tailored properties, meeting the demands of various applications such as microwave circuits, antenna designs, and sensor systems. This article explores the characteristics and advantages of different dielectric substrate materials and their wide-ranging applications in electronics, offering insights into selecting the right substrate for specific requirements.
What Are Dielectric Substrates?
Dielectric substrates are materials designed to influence electronic circuits’ electrical and electromagnetic behavior. Unlike conductive materials, they act as insulators, storing electrical energy without allowing current to flow. Their effectiveness is primarily measured by their dielectric constant (a higher value enables compact circuit designs) and loss tangent (lower values reduce signal energy loss).
These substrates provide mechanical stability to delicate circuit components and act as a medium for transmitting and shaping electromagnetic waves. Their properties directly affect the performance of devices such as antennas, filters, and resonators. For example, in high-frequency applications like 5G communication systems, the choice of substrate determines signal clarity and efficiency, making dielectric substrates indispensable in advancing modern electronics.
Common Dielectric Substrate Materials
Dielectric substrates come in a variety of materials, each offering unique properties to meet specific application needs. These materials are broadly categorized into ceramics, polymers, and composites, each tailored for distinct electronic and environmental demands.
Ceramic Substrates
Ceramic materials are widely recognized for their high dielectric constants, excellent thermal stability, and low loss tangents. Common examples include:
- Titanium Dioxide (TiO₂): Known for its high dielectric constant, TiO₂ is ideal for high-frequency circuits and microwave resonators.
- Alumina (Al₂O₃): A durable and thermally stable material, Al₂O₃ is commonly used in general-purpose electronics.
- Barium Titanate (BaTiO₃): With exceptional dielectric properties, BaTiO₃ is a preferred material for capacitors and high-frequency filters.
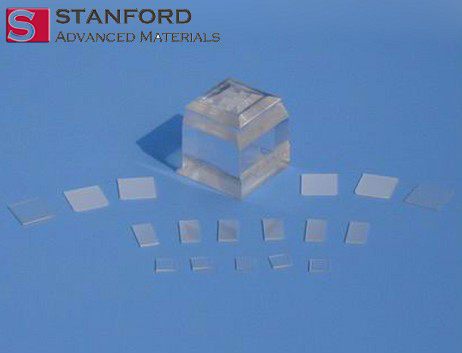
Polymer Substrates
Polymers are lightweight and flexible, making them suitable for applications requiring mobility and adaptability. Examples include:
- PTFE (Polytetrafluoroethylene): This polymer offers a low loss tangent, making it an excellent choice for microwave circuits and antennas.
- LCP (Liquid Crystal Polymer): Valued for its high-frequency performance, LCP is widely used in 5G and millimeter-wave applications.
Composite Materials
Composite substrates combine ceramics and polymers, striking a balance between performance and cost.
- Glass-Fiber Reinforced Composites: These materials are extensively used in printed circuit boards (PCBs) for general electronic devices.
- Nano-Composites: Engineered for high-frequency and high-power applications, these advanced materials offer superior performance in niche fields.
Each material type has its strengths and limitations, and the choice depends on the specific performance requirements of the application.
Material Performance Comparison
The performance of dielectric substrates depends on their physical and electromagnetic properties. Key factors to consider include dielectric constant, loss tangent, thermal stability, and mechanical strength. Below is a breakdown of these properties and how they influence substrate selection:
- Dielectric Constant (εr): A higher dielectric constant allows for compact circuit designs by enabling tighter spacing of components. However, excessively high values can introduce signal distortion, requiring careful optimization.
- Loss Tangent (tan δ): A low loss tangent is essential for minimizing energy loss in high-frequency applications, ensuring better signal clarity and efficiency.
- Thermal Stability: Substrates with high thermal stability, such as ceramics, are ideal for applications in extreme environments, where consistent performance under varying temperatures is critical.
- Mechanical Strength: Stronger materials like alumina and composite substrates provide durability and reliability in mechanically demanding applications.
Comparison Table
Material | Dielectric Constant | Loss Tangent | Thermal Stability | Mechanical Strength | Cost | Processing Complexity | Typical Applications |
---|---|---|---|---|---|---|---|
TiO₂ | High (~80-100) | Low | Excellent | High | High | High | High-frequency circuits, resonators |
Al₂O₃ | Moderate (~9-10) | Low | Excellent | Very High | Moderate | Moderate | General-purpose PCBs, industrial electronics |
BaTiO₃ | Very High (~120-150) | Moderate | Moderate | High | High | Moderate | Capacitors, filters, microwave devices |
PTFE | Medium (~2.0-2.5) | Very Low | Moderate | Low | Low | Low | RF antennas, low-cost consumer electronics |
LCP | Medium (~3.0-4.0) | Low | Good | Moderate | Medium | Moderate | 5G systems, millimeter-wave applications |
Glass Fiber | Low (~4.0-5.0) | Medium | High | High | Low-Medium | Low | PCBs for general electronics, cost-effective applications |
Nano-Composites | Variable | Low | High | Variable | High | High | Specialized high-frequency and high-power applications |
Selecting the right material requires balancing these properties to meet specific application needs. For instance, PTFE may be suitable for cost-sensitive projects in consumer electronics, while TiO₂ is preferred for high-performance systems in aerospace or telecommunications.
How to Select the Right Dielectric Substrate
Choosing the appropriate dielectric substrate depends on the specific requirements of the application. The following factors are critical in making an informed selection:
1. Application Requirements
- Frequency Range: High-frequency applications, such as 5G communication systems, demand materials with a low loss tangent (e.g., LCP or PTFE).
- Power Levels: For high-power systems, materials like TiO₂ or BaTiO₃ offer excellent thermal stability and performance.
2. Environmental Conditions
- Thermal Stability: Applications in harsh environments, such as aerospace or industrial electronics, require substrates like Al₂O₃ for their ability to maintain performance under extreme temperatures.
- Mechanical Durability: For automotive electronics or heavy-duty systems, glass-fiber composites provide a balance of strength and cost.
3. Cost and Manufacturability
- Budget Considerations: For cost-sensitive consumer electronics, materials like PTFE are an economical choice without compromising essential performance.
- Processing Complexity: Easily processed materials, such as polymers, are ideal for high-volume production, while ceramics may require advanced techniques for precision applications.
4. Example Selection Process
- Step 1: Define the application’s operating frequency, power level, and environmental constraints.
- Step 2: Match these requirements with materials based on their dielectric constant, loss tangent, and thermal properties.
- Step 3: Consider cost and ease of processing to finalize the selection.
For example, in a 5G antenna system, LCP is often chosen for its excellent performance at high frequencies and reasonable processing requirements. In contrast, for industrial sensors, Al₂O₃ offers the durability and stability necessary for reliable operation.
Conclusion
Dielectric substrates are foundational materials in modern electronics, influencing the performance and reliability of devices across industries. From telecommunications to aerospace, their ability to provide mechanical support and optimize electromagnetic properties ensures their critical role in advancing technology.
The diverse range of dielectric materials—ceramics, polymers, and composites—offers tailored solutions for specific applications, balancing properties like dielectric constant, loss tangent, and thermal stability. Selecting the right substrate requires careful evaluation of application requirements, environmental conditions, and budget considerations.
With a comprehensive portfolio of high-performance dielectric substrates, Stanford Advanced Materials (SAM) is a trusted supplier for industries worldwide, offering materials designed to meet the most demanding specifications. Contact SAM today to discover the ideal substrate for your next project.