Introduction
Evaporation coatings are a crucial technology in various high-tech industries, offering protective and functional layers to multiple products. Among the materials used in evaporation coatings, hafnium particles stand out for their unique properties and benefits. This article explores the use of hafnium particles in evaporation coatings, focusing on their importance, properties, and benefits for various industries.
Properties of Hafnium Particles
Hafnium (Hf) is a transition metal known for its impressive chemical and physical properties. With a high melting point of 2,233°C and excellent corrosion resistance, hafnium is particularly suited for demanding applications.
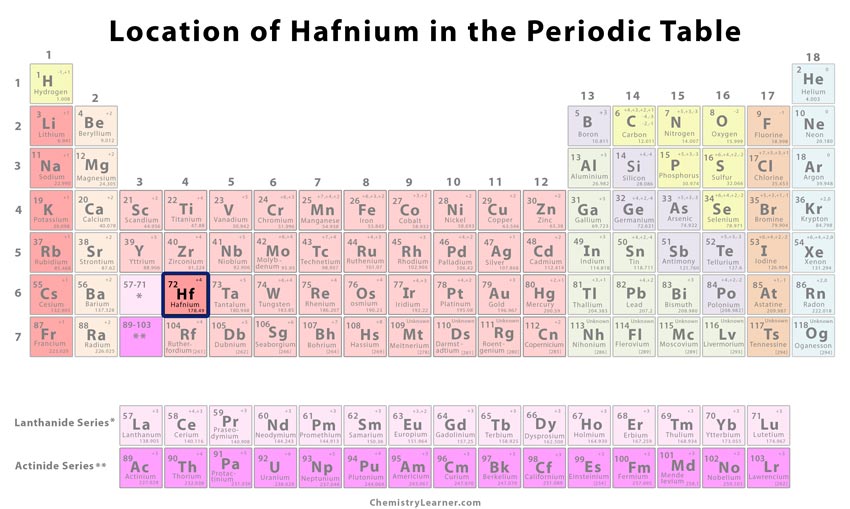
Chemical and Physical Properties:
- Atomic number: 72
- Density: 13.31 g/cm³
- High melting and boiling points
- Exceptional corrosion resistance
Advantages of Using Hafnium:
- Stability at high temperatures
- Resistance to chemical reactions
- Excellent hardness and durability
Compared to other materials, hafnium’s ability to withstand extreme conditions makes it ideal for specialized coatings in critical applications.
Applications of Hafnium Particles in Evaporation Coatings
Evaporation coating is a process where material is vaporized and deposited onto a substrate, forming a thin film. Hafnium particles are increasingly used in this process due to their advantageous properties.
Industries and Products:
- Aerospace: Hafnium coatings protect components from high temperatures and oxidation, extending their lifespan and performance.
- Electronics: Used in semiconductor devices, hafnium coatings enhance electrical properties and reliability.
- Optical Coatings: Hafnium is utilized in the production of lenses and mirrors, improving durability and optical clarity.
- Medical Devices: Hafnium coatings provide biocompatibility and wear resistance, essential for implants and surgical instruments.
Benefits of Hafnium-Based Coatings
Hafnium-based coatings offer several key benefits that make them superior to conventional materials.
Enhanced Durability and Corrosion Resistance: Hafnium coatings provide a robust barrier against wear and corrosion, significantly extending the life of the coated products.
Improved Performance in High-Temperature Environments: With their high melting point and thermal stability, hafnium coatings maintain their integrity under extreme heat, making them ideal for aerospace and industrial applications.
Superior Adhesion and Coverage: Hafnium particles create a uniform and adherent layer, ensuring complete coverage and effective protection of the underlying substrate.
Technical Considerations
Applying hafnium coatings requires precise techniques to achieve the desired properties and performance.
Methods of Application:
- Physical Vapor Deposition (PVD): A popular method where hafnium is vaporized in a vacuum chamber and deposited onto the substrate.
- Chemical Vapor Deposition (CVD): Involves chemical reactions to form a hafnium layer on the surface.
- Sputtering: Uses ionized gas to dislodge hafnium atoms, which then coat the substrate.
Challenges and Solutions:
- Uniformity: Achieving a consistent coating requires meticulous control of deposition parameters.
- Adhesion: Surface preparation and choice of deposition method are critical to ensure strong adhesion.
Quality Control and Standards: Maintaining high standards in the coating process ensures the reliability and effectiveness of hafnium coatings. Regular inspections and adherence to industry standards are essential.
Case Studies
Example 1: Aerospace Industry
A leading aerospace manufacturer faced challenges with the durability and performance of turbine blades used in jet engines. These components are exposed to extremely high temperatures and corrosive environments, which can lead to wear and failure over time. To address these issues, the manufacturer decided to implement hafnium-based coatings on the turbine blades.
The results were remarkable. The hafnium coatings provided exceptional thermal stability and resistance to oxidation, which significantly enhanced the blades’ durability. The manufacturer observed a 20% increase in engine efficiency due to the improved performance of the coated blades. Additionally, the frequency of maintenance and replacements dropped significantly, leading to substantial cost savings and increased operational uptime.
Example 2: Medical Devices
A prominent medical device company sought to improve the biocompatibility and longevity of its surgical instruments. These instruments are subject to rigorous sterilization processes and repeated use, which can degrade their performance and increase the risk of infections.
The company opted for hafnium coatings to address these concerns. The coatings provided a robust barrier against corrosion and wear, which enhanced the instruments’ durability. More importantly, the biocompatible nature of hafnium minimized the risk of adverse reactions in patients. As a result, the instruments demonstrated a higher resistance to sterilization-induced degradation and maintained their integrity over extended use. This led to a reduction in infection rates and improved patient outcomes, solidifying the company’s reputation for high-quality medical devices.
Conclusion
Hafnium particles play a vital role in the advancement of evaporation coatings, offering unparalleled benefits in durability, performance, and versatility. As industries continue to push the boundaries of technology, hafnium coatings are poised to become even more integral. For more information on hafnium coatings and to explore how they can benefit your products, contact us at SputterTargets.net.