I. Introduction
High-entropy alloys (HEAs) represent a paradigm shift in alloy design. Unlike traditional alloys that rely on a dominant elemental component, HEAs are composed of five or more principal elements in near-equiatomic or equimolar ratios. This unique composition results in high-entropy solid solutions with superior properties not achievable by conventional alloys. The concept of HEAs was officially introduced in the early 2000s, and since then, extensive research has been conducted to explore their potential applications and benefits.
This article delves into the role of high-energy alloy sputtering targets in thin film deposition and coating processes. It examines the definition and characteristics of HEAs, highlights their advantages over traditional alloy targets, explores their applications in thin film technologies, and provides a comparative analysis with conventional materials such as copper and gold targets. Additionally, considerations for selecting HEA targets and their significance in the future of materials science are discussed.
II. Definition and Characteristics of High-Entropy Alloys
High-entropy alloys are defined by their multi-component composition, typically incorporating five or more elements. These elements are present in equiatomic or near-equimolar ratios, with each contributing approximately 5% to 35% of the total atomic composition. This broad compositional range allows for the inclusion of various ternary and quaternary alloys, enabling a vast array of possible combinations and tailoring properties to meet specific application requirements.
HEAs exhibit several distinctive features that set them apart from traditional alloys:
-
High-Entropy Solid Solutions: The substantial configurational entropy arising from the multiple principal elements stabilizes the solid solution phases, often forming simple crystalline structures such as face-centered cubic (FCC), body-centered cubic (BCC), or hexagonal close-packed (HCP).
-
Lower Diffusion Coefficients: The complex atomic interactions and lattice distortions in HEAs result in reduced atomic mobility, leading to lower diffusion coefficients. This characteristic enhances the high-temperature stability of HEAs.
-
Solid Solution Strengthening: The presence of multiple elements in HEAs creates a highly disordered lattice, impeding dislocation movement and thereby increasing the material’s strength and hardness.
-
Optimized Alloy Properties: The synergistic effects of the constituent elements enable HEAs to achieve a combination of desirable properties, including mechanical strength, corrosion resistance, and thermal stability, that are often unattainable in traditional alloy systems.
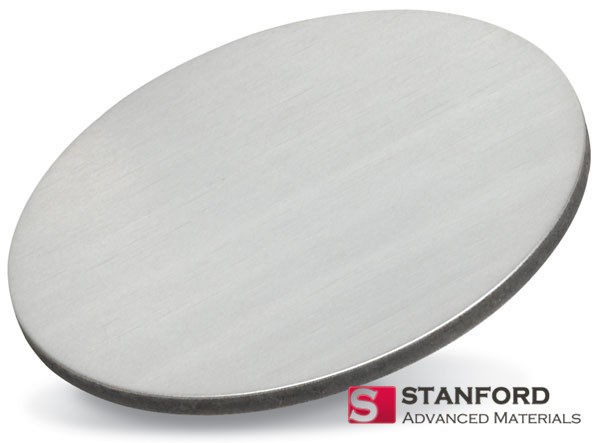
III. Advantages of High-Entropy Alloy Targets
A. Enhanced Mechanical Properties
HEAs are renowned for their superior mechanical properties. The complex composition and solid solution strengthening mechanisms confer higher hardness and improved fatigue resistance compared to traditional alloys. This makes HEAs particularly suitable for applications requiring materials that can withstand substantial mechanical stress and wear.
B. Superior Corrosion Resistance
The uniform distribution of multiple elements in HEAs leads to enhanced corrosion resistance. This uniformity ensures that no single element dominates the surface chemistry, resulting in stable behavior in oxidizing and acidic environments. Such properties are invaluable for protective coatings in harsh operational settings.
C. Excellent Thermal Stability
HEAs maintain their structural integrity at elevated temperatures due to their stable crystal lattice structures and reduced diffusion rates. This thermal stability makes HEA targets ideal for thin film deposition processes that operate under high-temperature conditions, ensuring consistent performance and longevity of the coatings.
D. High Customizability
One of the most significant advantages of HEAs is their high degree of customizability. By varying the constituent elements and their ratios, HEAs can be tailored to exhibit specific properties suited to diverse applications. This versatility expands the potential use cases of HEA targets across various industries.
IV. High-Entropy Alloy Targets in Thin Film Deposition and Coating
In thin film deposition and coating processes, the quality and properties of the target material directly influence the characteristics of the resulting films. HEA targets offer exceptional stability and thermodynamic properties, enabling the production of high-performance thin films with superior uniformity and adherence. The multi-element composition of HEAs facilitates the formation of complex, multifunctional coatings that can meet stringent application demands.
HEA targets are employed in various thin film deposition techniques, including Physical Vapor Deposition (PVD), Magnetron Sputtering, and Electron Beam Deposition. These techniques are used to apply coatings that require exceptional hardness, corrosion resistance, and thermal stability, such as protective coatings for cutting tools, aerospace components, and electronic devices.
Utilizing HEA targets in thin film deposition results in coatings with enhanced material properties. These coatings exhibit improved longevity, reduced wear and tear, and better performance under extreme conditions compared to those derived from traditional targets. The ability to customize the HEA composition allows for precise tuning of the coating properties to meet specific application requirements.
V. Comparison Between High-Entropy Alloy Targets and Traditional Targets
A. Traditional Targets Overview
Traditional alloy targets, such as copper and gold, have long been used in thin film deposition and coating applications. Copper targets are favored for their high thermal and electrical conductivity, making them suitable for electronic applications. Gold targets are prized for their excellent reflectivity and corrosion resistance, often used in decorative coatings and electronics. However, these traditional targets have inherent limitations, including lower mechanical strength, limited corrosion resistance beyond specific environments, and restricted customizability.
B. Comparative Analysis
VI. Advantages of High-Entropy Alloy Targets Over Traditional Targets
-
Enhanced Resistance to Mechanical Stress: HEA targets provide coatings with superior hardness and fatigue resistance, making them ideal for applications subjected to repetitive mechanical stresses.
-
Superior Corrosion Resistance: The multi-element composition ensures that HEA-based coatings remain stable and resistant to corrosion in a wider range of environments compared to traditional materials.
-
Improved Thermal Stability: HEA targets maintain their structural integrity and performance at higher temperatures, reducing the risk of degradation during high-temperature processing or operational conditions.
-
Greater Customizability and Versatility: The ability to tailor the elemental composition of HEAs allows for the design of coatings with specific properties, enhancing their applicability across diverse fields.
-
Potential for Advanced Applications: HEA targets open avenues for innovative applications in emerging technologies, including advanced electronics, aerospace components, and biomedical devices, where superior material performance is critical.
VII. Considerations for Choosing High-Entropy Alloy Targets
A. Performance Requirements
When selecting HEA targets, it is essential to consider the specific property requirements of the intended application. Factors such as mechanical strength, corrosion resistance, and thermal stability should align with the performance needs.
B. Application Environment
The operational environment, including temperature ranges, exposure to corrosive agents, and mechanical stresses, must be evaluated to ensure that the chosen HEA composition can withstand these conditions effectively.
C. Cost-Effectiveness
While HEAs offer superior properties, their cost relative to performance benefits must be assessed. The selection process should balance material costs with the anticipated performance improvements and longevity of the coatings.
D. Manufacturing and Processing Factors
Compatibility with existing deposition and manufacturing techniques is crucial. HEA targets should be compatible with the chosen thin film deposition methods, and considerations regarding ease of fabrication and scalability should be taken into account.
VIII. Conclusion
High-entropy alloy (HEA) Targets signify a pivotal advancement in materials science, offering superior mechanical strength, exceptional corrosion resistance, and remarkable thermal stability compared to traditional alloy targets. Their versatility in composition allows for tailored properties, making them ideal for a wide range of thin film deposition and coating applications. As industries continue to demand higher-performance materials, HEA targets present a promising solution, facilitating the development of durable and efficient coatings for sectors such as aerospace, electronics, and biomedical engineering. Moving forward, ongoing research and optimization of HEAs will further unlock their potential, solidifying their role in the future of advanced material technologies.
Stanford Advanced Materials (SAM) specializes in providing high-quality HEA target materials, supporting various industries in achieving their coating and deposition needs. By offering a diverse range of HEA targets, SAM facilitates the integration of these advanced materials into cutting-edge applications, thereby contributing to the continued advancement and adoption of HEA technologies across multiple sectors.