Chemical Vapor Deposition (CVD) is a widely used technique that plays a critical role in various industrial applications. This method involves depositing thin films of material onto a substrate, often at high temperatures, through chemical reactions. The flexibility of CVD allows it to be employed in diverse fields ranging from glass coatings to the fabrication of semiconductors. This article explores the applications of CVD technology in different industries and highlights its significant contributions to material development.
1. CVD in Glass Coatings
One of the most prominent applications of CVD technology is in the glass coating industry, particularly for producing high-performance glass surfaces. During the float-glass manufacturing process, glass sheets pass through a molten tin bath, where they undergo controlled temperature changes. The CVD method is employed to deposit a thin, durable layer on the glass surface, improving its hardness and resistance to wear.
Typically, a mixture of silane gas and nitrogen is used in CVD to produce silicon coatings. These coatings offer numerous advantages, such as increased durability, enhanced resistance to scratches, and better optical properties. The controlled deposition of silicon also prevents oxidation, making it ideal for the production of advanced glazing and energy-efficient windows.
2. CVD in Aerospace and Automotive Industries
In aerospace and automotive manufacturing, CVD is used to create protective coatings that enhance the performance and longevity of various components. By applying CVD coatings to metal surfaces, manufacturers can improve resistance to corrosion, wear, and high temperatures. This is particularly valuable for parts exposed to extreme conditions, such as engine components, turbine blades, and exhaust systems.
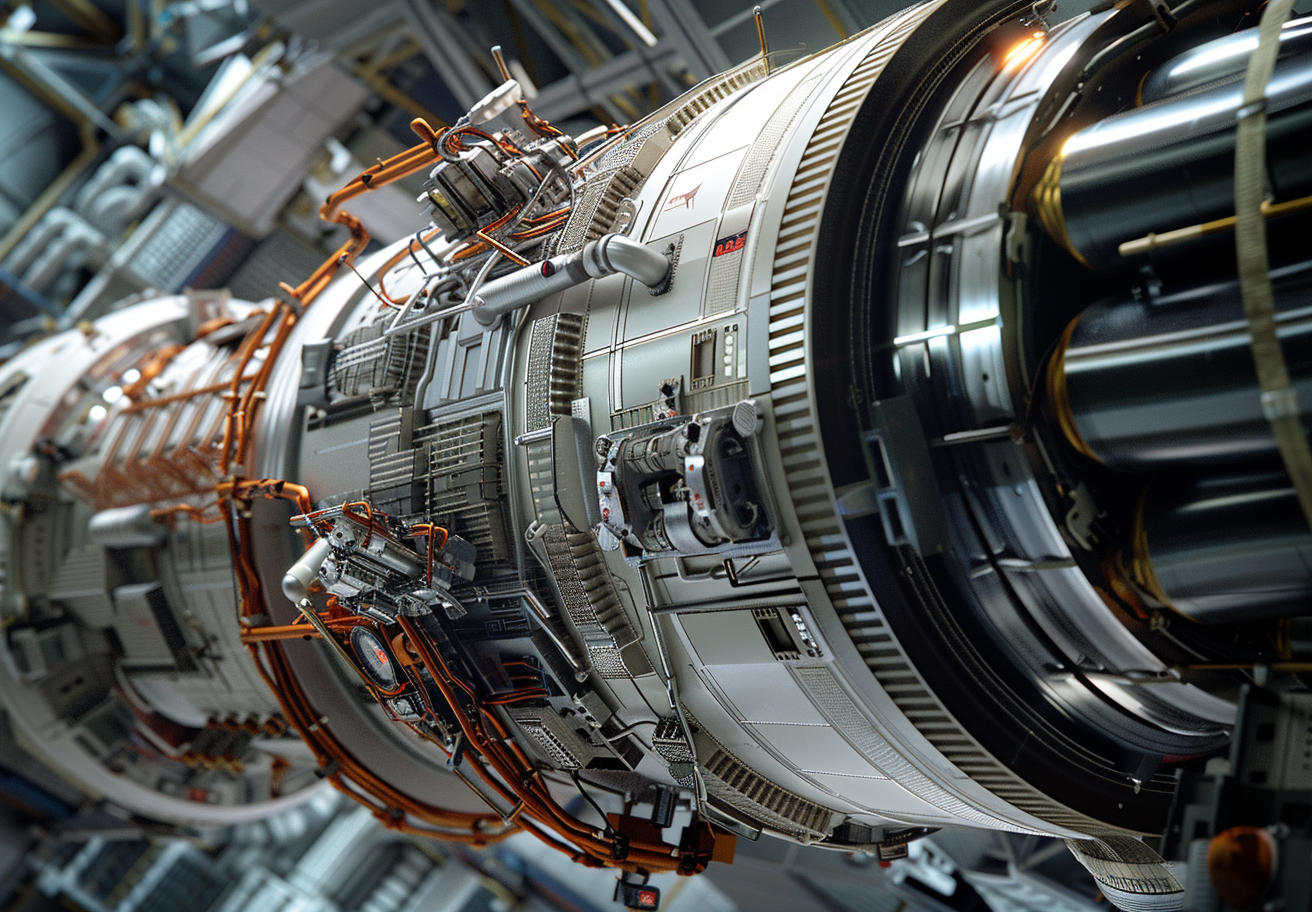
CVD coatings can also enhance the adhesion of composite materials and reduce friction, leading to better fuel efficiency and improved performance in both automotive and aerospace systems. The ability to tailor the composition and thickness of coatings through CVD ensures that these industries benefit from high-performance materials capable of withstanding harsh operational environments.
3. CVD in the Semiconductor Industry
One of the most crucial applications of CVD is in the semiconductor industry, where it is used to deposit thin films for integrated circuits (ICs) and electronic devices. CVD is essential in creating the insulating, conductive, and semiconducting layers that form the building blocks of modern electronic systems. By carefully controlling the process, manufacturers can produce uniform and defect-free thin films, ensuring the reliability and performance of advanced semiconductors.
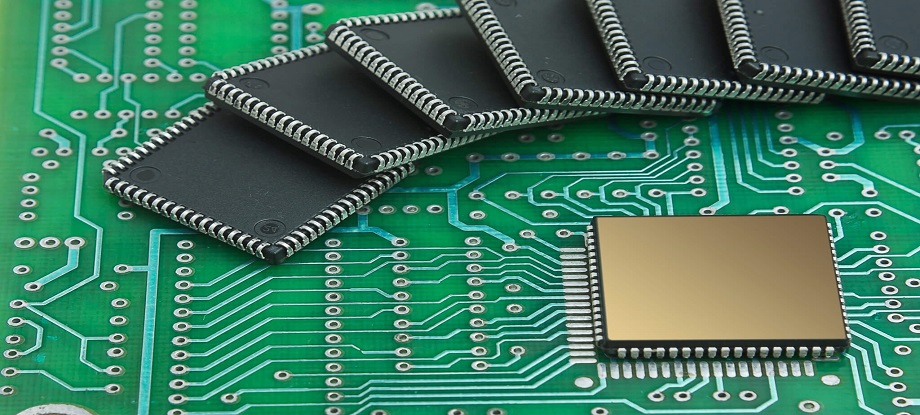
CVD also plays a vital role in the production of light-emitting diodes (LEDs) and solar cells, where high-quality thin films are necessary for efficient light conversion and energy harvesting. As the demand for smaller, faster, and more energy-efficient devices increases, the precision offered by CVD remains a key technology in meeting these needs.
4. CVD in Electronics and Solar Cells
Electronics Manufacturing
In electronics, CVD technology is indispensable for fabricating components such as transistors and capacitors. The deposition of materials like silicon, silicon nitride, and various metal films using CVD ensures the creation of thin, uniform layers with high purity. This is crucial for the high-performance demands of modern electronics, from microprocessors to wearable devices.
CVD enables the fabrication of intricate patterns and devices at the nanoscale, allowing for further miniaturization of electronic components. The precision of CVD deposition provides superior material quality, contributing to the enhanced functionality and durability of electronic products.
Solar Cells
CVD also plays a significant role in the production of thin-film solar cells. These solar cells are made by depositing photovoltaic materials, such as cadmium telluride (CdTe), copper indium gallium selenide (CIGS), and amorphous silicon, onto substrates using CVD. The ability to control film thickness and composition is critical to optimizing the efficiency of solar cells.
As renewable energy solutions become more widely adopted, CVD technology continues to improve the performance and cost-effectiveness of solar cells. The high efficiency and scalability of CVD processes are making solar energy a more viable option for mass production and use, contributing to the global transition to cleaner energy sources.
5. CVD in Cutting Tools and Tool Coatings
Another important application of CVD is in the enhancement of cutting tools and industrial machinery. CVD is commonly used to deposit hard and wear-resistant coatings on tools such as drills, milling cutters, and inserts. These coatings are typically made from materials like titanium nitride (TiN), cubic boron nitride (CBN), and diamond-like carbon (DLC).
By applying these coatings, manufacturers can significantly extend the lifespan of cutting tools, reduce friction, and improve the efficiency of machining operations. CVD coatings also provide thermal protection, allowing tools to perform at higher temperatures without degrading. This makes CVD-coated tools ideal for high-precision machining and heavy-duty industrial applications.
6. CVD for Single-Crystal Metal Oxides and Net-Shape Products
CVD is also essential in the production of single-crystal metal oxides, such as sapphire and iron oxides. These materials have a wide range of applications, from optoelectronic devices to magnetic and catalytic systems. The CVD process allows for the precise growth of these materials, ensuring their high purity and structural integrity.
Moreover, CVD is used to create net-shape products, such as tubes and crucibles, by depositing layers of material onto a substrate and then removing the base layer to leave a final, standalone product. This capability allows for the production of complex shapes with high precision and minimal waste, making CVD a valuable tool in advanced manufacturing processes.
7. Conclusion
CVD technology has proven to be a versatile and indispensable method across various industries, from glass coatings and semiconductors to aerospace, automotive, and electronics. Its ability to control thin-film deposition with high precision ensures that materials and components exhibit superior performance, durability, and efficiency. As industries continue to evolve, the role of CVD in material science and manufacturing will only grow, driving innovation and contributing to advancements in technology and sustainability. For more detailed insights into CVD and its applications, visit https://www.sputtertargets.net/.